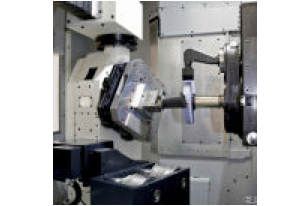
Built by the Japanese firm, Makino, the 7-axis G7 i-Grinder is based on a machining centre platform. This allows other metalcutting tools such as milling cutters, drills, broaches and turning tools to be exchanged automatically between the tool magazine and the spindle, allowing additional machining operations to be carried out in the same cycle. The VIPER process patented by Roll-Royce was first introduced in 2001.
An improvement over Makino's smaller G5, i-Grinder model, the G7 uses two roll stacks to dress the grinding wheels. This allows the flexibility to produce a greater variety of components without having to change the rolls, reducing unproductive time and better suiting the machine to an automated production cell environment.
In the case of some complex components like turbine vanes, more than three operations may be needed. Usually, three is the maximum number of grinding wheel profiles a dressing roll stack can hold.
On a G5, components requiring four or more operations therefore have to be part machined in batches to achieve economical manufacture and then returned to the machine for another set-up, with consequent work in progress, wasted time and potential for loss of accuracy.
By contrast, on the G7 such parts can be machined in one visit to the machine, so one-off production is economical.
Metal removal rate is of the order of 80cc/minute. Grinding efficiency comes from a number of factors, including linear rapid traverse rate of 48m/minute and a fast rotary workhead speed of 100rpm, especially beneficial when processing smaller components.
Noteworthy is the design of the programmable coolant nozzles which may be positioned by two rotary NC axes anywhere through 360° around the periphery of the grinding wheel. Nozzle positioning is fast and responsive when changing orientation to ensure that coolant continues to be accurately directed towards the point of cutting at all times.
Supporting offline programming of the G7 and transfer of cycles to the grinder are two pieces of specific software from Makino-NCMT, namely the EasyGrind CAM package and EasyCorrect, which runs in a human machine interface attached to the machine.
The Makino i-Grinder G5 accepts parts nominally up to 300mm in diameter, but with increasing aircraft engine sizes, some larger vanes were falling outside the machine's working envelope. The G7's X- 730mm x Y- 650mm x Z-axis 730mm capacity addresses the problem and also brings the smaller end of industrial gas turbine components within its scope.
The first G7 has already been sold to the Årjäng factory of Hanza Precision AB in Sweden for the manufacture of industrial gas turbine blades and vanes. The turnkey cell, which marks the Swedish company's first use of VIPER grinding, has been automated with the addition of a Fanuc robot for unattended machining. |